Because this product does not carry or discharge static electricity, the addition of an ionizer or other neutralizing equipment is not necessary. This makes it possible to dependably handle precision product workpieces.
High precision porous ceramic vacuum chuck "aeroFIX".
Lifts, Holds and Carries
With improvements in miniaturization and high-precision technologies, and higher performance of solar cells, LEDs, semiconductors, LCDs, organic EL, PCBs, and a broad range of other products, there is growing need for vacuum chucks that deliver higher levels of precision and performance.
The aeroFIX developed by NanoTEM is a completely new type of vacuum chuck that utilizes our original ceramic sintering technology to resolve the issues facing conventional through-hole type vacuum chucks!
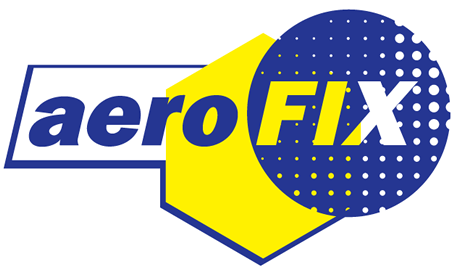